Solutions for Safer, Faster Turnarounds
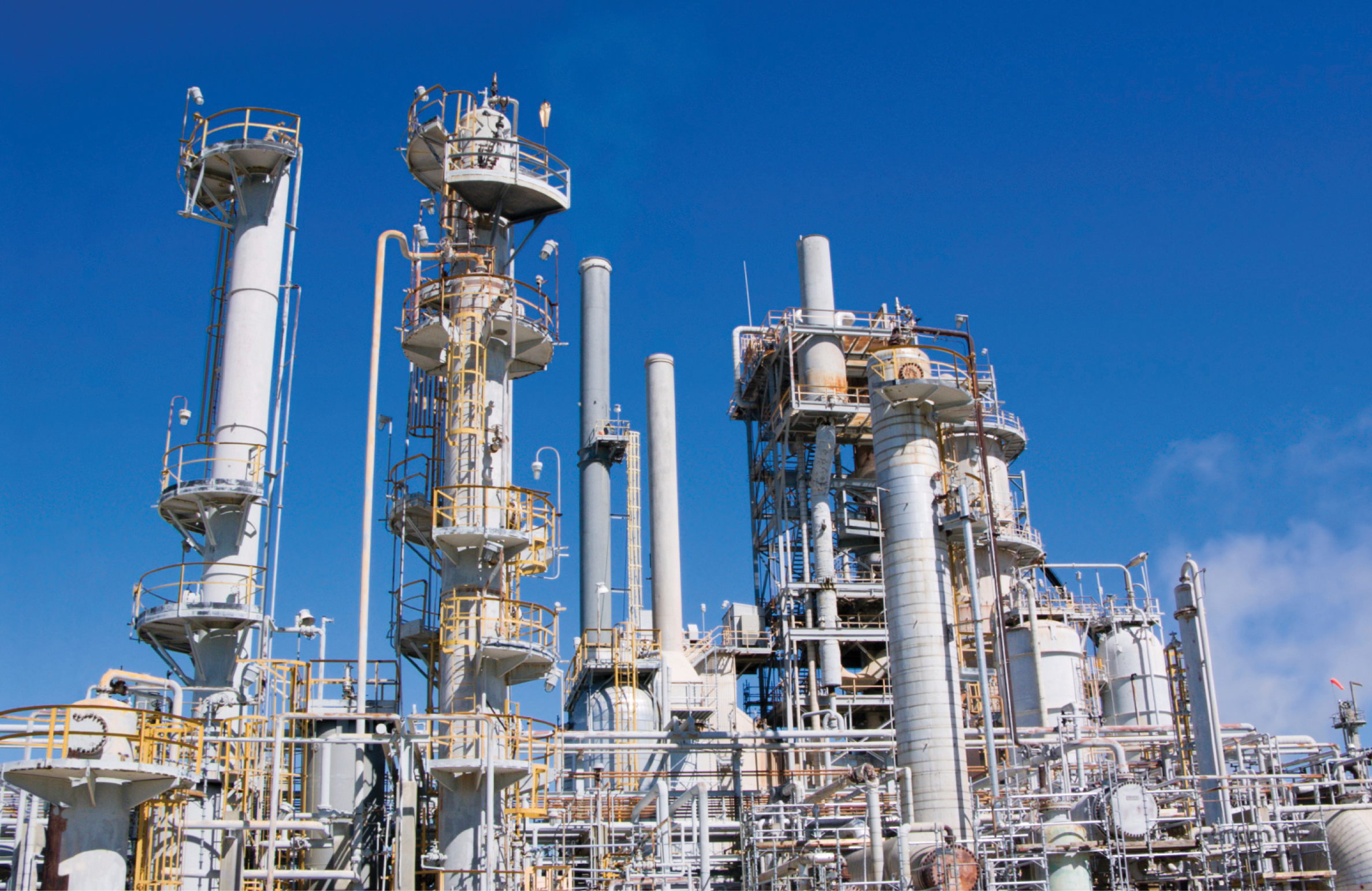
Applications
FCC and alky units, crude and heavy oil units
Coker units, sat gas and sour water strippers
Amine, sulfur recovery, visbreaker, platformer, and hydrobon units
Desalters, caustic treaters, exchangers and overhead condensers
Boilers and cooling water systems, fuel gas systems, storage tanks
Quench water systems, pre-op cleaning, small tanks and knockout drums
Complete flare systems, complete glycol and gas plant systems
Plastic and polymer removal using proprietary polymer extraction process (PEP)
Steam blow of piping systems, foam cleaning
Veteran Expertise
Our team provides a customized plan for engineering and operational support that provides maximum value for you. What’s more, we have the ability to execute projects while making informed critical path decisions and overcoming unexpected challenges. We follow up with post-project reporting on lessons learned and opportunities for future improvement.
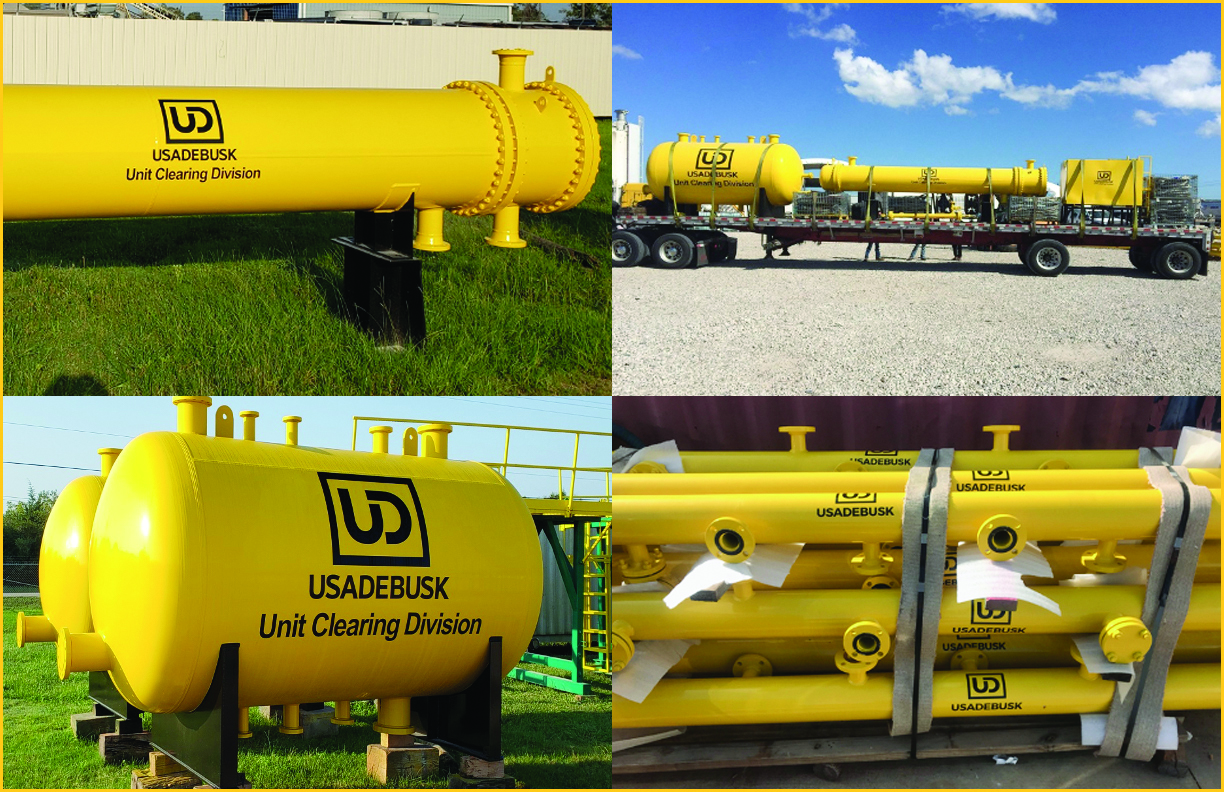
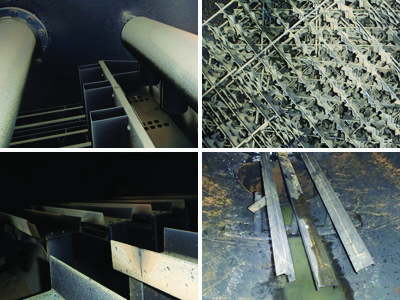
Advanced Chemistries
We offer proprietary products designed for the neutral pH cleaning of HF Alkylation units and other process equipment that have issues with polymers, scales or other foulants that negatively affect production. These options provide a long list of benefits over the mineral acids or other less effective commodity methods. Our treatment methods and designs always provide significant safety protection and cost reduction.
Patented KixSolv® is a concentrated chemical cleaner designed to remove hydrocarbon-based contaminants and noxious gases from process equipment internals. It is a proprietary blend of hydrocarbon solvents and specialty additives.
The primary application for KixSolv® is in a steam vapor phase process to clean equipment and allow opening to the atmosphere. When equipment is shut down and entry is needed, this product is injected to remove hydrocarbon liquids and solids from equipment and to clear LEL, H2S, benzene and other noxious gases. KixSolv® is also applied to remove hydrocarbon foulants, improving heat transfer in exchangers and decreasing equipment pressure drop.
Advantages
- Fast reduction of LEL, H2S, benzene and other noxious gases
- Excellent internal surface cleaning of organic material
- Better cleaning at lower cost than terpene-based products
- Reduced shutdown timeline
- Worry-free effluent processing
- Superb metallurgical compatibility
Key Features
- Strong solvency for hydrocarbon contaminants, including heavy hydrocarbons and tars
- Excellent penetration and removal of hydrocarbon foulants
- Significantly more powerful than terpene-based products
- Short chemical injection time when used with a steam vapor phase process
- Cleaning effluent can easily be reprocessed with no product quality issues
KixClear® improves reactor clearing processes by eliminating hydrocarbon-based contaminants and noxious gases. This application, which is integrated into the shutdown procedure, results in faster shutdown timelines from oil-out until blinding and provides more certainty with planning schedules. The product does not contain any substances such as water or metals that are potentially harmful to catalysts.
KixClear® application improves the timeline, certainty, and quality of clearing reactors during shutdowns. During the reactor shutdown procedure, KixClear® is injected to remove hydrocarbon contaminants and clear LEL, H2S, benzene, and other noxious gases. KixClear® is also applied to remove hydrocarbon foulants to decrease reactor bed pressure drop and in other types of packed bed vessels where steam/water is not preferred.
Advantages
- Faster reactor shutdown timeline
- Decreased nitrogen usage and flaring
- Increased scheduling certainty
- Cleaner high-pressure equipment
- No harmful effects on catalyst
- Elimination of hot hydrogen stripping
Key Features
- Clears LEL, H2S, and other contaminants from reactor catalysts and the entire high pressure system
- Excellent at penetrating and removing hydrocarbon foulants
- Short chemical injection time
- Non-toxic and biodegradable
- Exceptional metallurgy and catalyst compatibility
- Cleaning effluent easily reprocessed with no product quality issues
Remedi® is used to treat pyrophoric material in process equipment. It is a proprietary blend of nonhazardous and biodegradable ingredients designed to eliminate all pyrophorics within a steam environment. This vapor phase application approach decreases treatment timelines and effluent volumes.
The primary application for Remedi® is in a steam carrier immediately after cleaning for LEL, H2S, and benzene is completed. Most frequently this is utilized for drums, exchangers, demister pads, and piping, where liquid treatment would be impractical. After hydrocarbons are removed, the chemical treats equipment for pyrophorics before opening to the atmosphere. This product can also be applied with other gas carriers such as nitrogen or in liquid form.
Advantages:
- Application during steaming decreases timeline and effluent volumes
- Large drums, overhead systems, and demister pads can be treated without water filling
- Positive verification of completion
- Easy effluent processing
- Excellent metallurgical compatibility
Key Features:
- Can be applied with steam
- Compatible with hydrocarbon material
- Non-reversible treatment of iron sulfide and other pyrophoric materials in the equipment
- Cleaning effluent can easily be processed with no product quality issues
- Simple test for completion
Fast-acting, Effective
The unique chemistry dissolves polymer deposits uniformly, without dislodging large pieces that can plug flow paths downstream. PlastEx has a high boiling point and low vapor pressure to react quickly and thoroughly with polymer deposits.
Non-toxic
PlastEx is extraordinarily safe and is classified by OSHA as non-hazardous and non-carcinogenic. PlastEx is also FDA compliant for food packaging. It is not regulated by the Department of Transportation (DOT) for air, land, or water, and no special personal protective equipment is required at ambient conditions. As a result, it is a safer option for personnel, as well as simpler and cheaper to transport, prepare, and apply.
Worry-free Disposal
Material from the PEP process is recovered and, depending on customer objectives, typically separated into liquid chemical and solid polymer components. Recovered chemical is available for reuse. Any liquid effluent from the process is minimal, requires no special handling and is considered non-hazardous material suitable for disposal in plant wastewater treatment systems. Solid polymer recovered from the process is ready for recycling or for disposal as nonhazardous waste.
Environmentally Responsible
PlastEx is readily biodegradable and non-toxic to aquatic organisms. Under normal conditions, no special breathing protection is required for those working with or near a PEP project. The PEP process generates minimal odors, benefitting both plant personnel and the surrounding community.
Higher Flash Point
PlastEx is safer to use, with a flash point of 210 F (99 C). It is classified as a National Fire Protection Association (NFPA) Class IIIB combustible liquid with a hazard rating of 1 for flammability.
KixSolv® Decontamination Chemistry
Vapor Phase Cleaning
Committed To Safe Operations
We consistently and frequently review policies, procedures and preventative incident practices to enhance our best-in-class safety culture. Other aspects of our safety culture include:
Dedicated safety team with highly qualified, credentialed personnel
Custom-built EHS system to manage audits/inspections, compliance obligations, incidents, corrective actions and more
Open, consistent, and clear communication to enforce audit expectations at every level
Rigorous orientation, refresher courses, and continuous on-job/off-job training
Commitment to automation to remove employees from hazardous areas
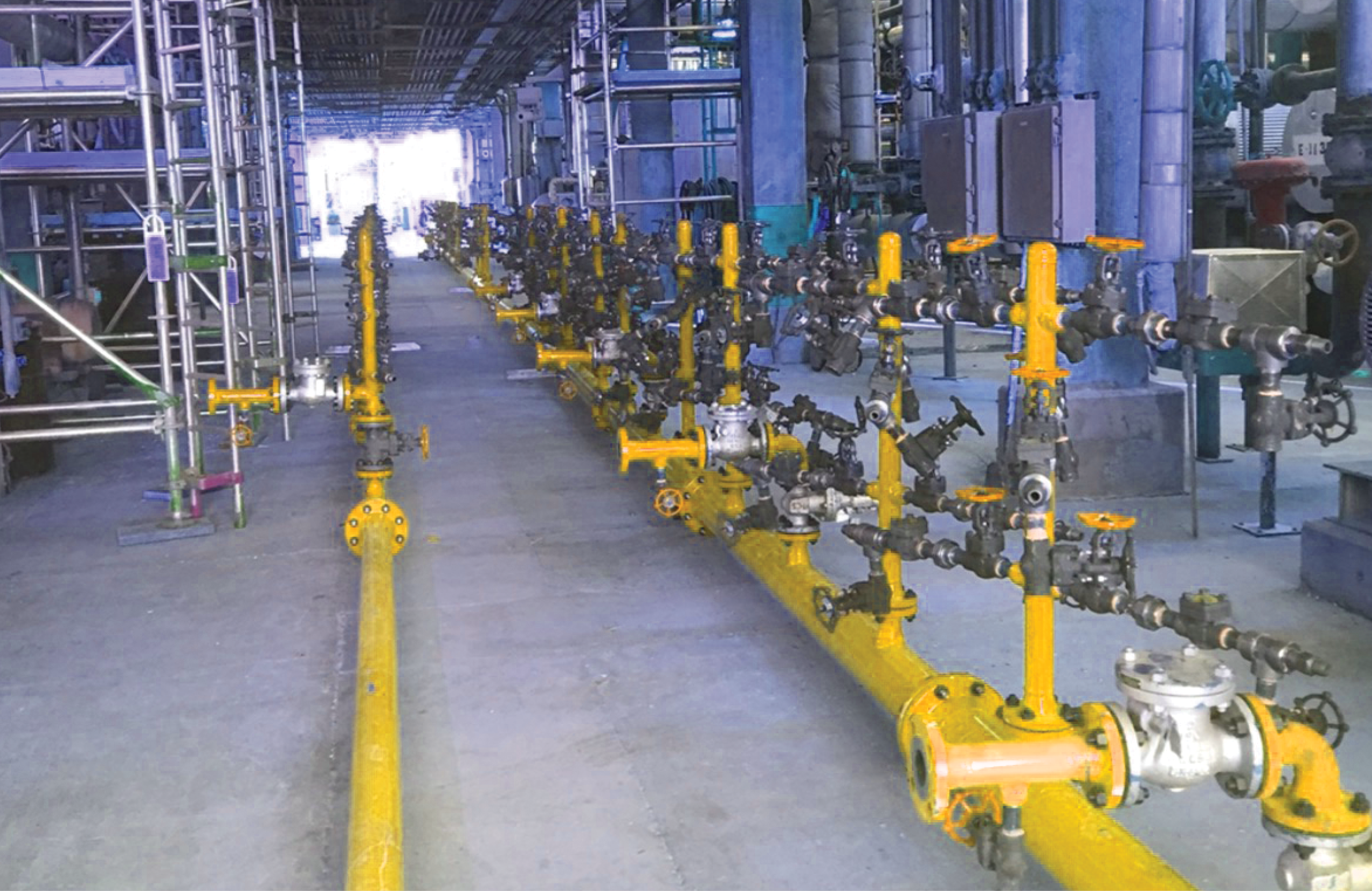