Specialized Technologies to Improve Maintenance & Operations
USA DeBusk offers proven specialty technologies to improve the safety, speed, and cost-effectiveness of daily maintenance and operations activities in offshore oil and gas applications.
Each technology offers unique advantages to address the rugged conditions, extreme space limitations, and demanding environmental requirements of offshore operations.
VAPOR BLAST
To meet continuing needs for surface preparation. inspection, repairs, and coating, USA DeBusk offers Vapor Blast, a patented [US Patent No. 11,933,556 B1] low-pressure water/abrasive vapor technology that is safe, dust-free, effective, and versatile.
COATING SERVICES
Integrated surface preparation and a full scope of coating techniques streamline project timelines and ensure superior-quality work.
NITROGEN SERVICES
On-site nitrogen generation ensures a ready supply of nitrogen gas for well services, purging, pigging, inerting, pressure testing, leak testing, and other routine activities. We also offer specialized nitrogen-based services for hydrate remediation and artificial lift.
Service Highlights
Our turnkey, multi-service-line solutions include these services and specialty technologies.
Vapor Blast
Vapor Blast is a patented [US Patent No. 11,933,556 B1], highly efficient cleaning and finishing process to prepare surfaces for recoating or to polish weld seams or other critical areas for inspection. Combining the effectiveness of both abrasive blasting and water washing, Vapor Blast yields equal or better results in a process that is safer, faster, more economical, and more practical than dry (sand) blasting, brushing, needle gunning, and grinding.
With Vapor Blast, abrasive media are mixed with water, direct-injected under hydraulic pressure into an airstream, and discharged through a hose and nozzle. A control system allows fine-tuning of flow rates and abrasive concentrations for optimum results. Atomized particles conveyed at low pressure produce controlled, uniform scrubbing action, even on hard-to-reach surfaces. A rust inhibitor can be added to the vapor stream to mitigate flash rust or corrosion in offshore environments.
Capabilities
Removes resins, rusts, chlorides, coatings, oils, stains, epoxy, mill scale and other contaminants, as well as scratches and grinding marks
Achieves 3.5 or better profile for paints and coatings
Performs one-pass polishing for IRIS and Eddy inspections
Cleans weld areas prior to API inspections
Removes CUI (Corrosion Under Insulation)
Allows simultaneous cleaning and rust inhibitor application
Extended reach, effectively cleaning up to 225 ft (even vertical) from the pumping unit
PRODUCTIVITY & EFFICIENCY
On average, Vapor Blast uses approximately 40 lb of media per hour, while sandblasting uses between 1000-1,500 lb of media per hour. Reduced media requirements saves space, reduces consumables costs, and substantially reduces cleanup time and waste volume. With no dust cloud, Vapor Blasting can be performed within 10 ft of other work without interference.
A Vapor Blast project occupies a small footprint and has limited containment requirements. It also allows extended access without repositioning equipment. Hoses can be run up to 225 ft from the pumping unit (horizontal and vertical).
SAFETY & ENVIRONMENTAL
The environmentally safe abrasives used in Vapor Blast are the only media to pass the Fish and Shrimp Kill Test. They contain no detectable silica (<0.1%). Unlike dry blasting, Vapor Blast produces no dust, complies with OSHA permissible airborne silica exposure levels, and prevents hot sparks from static electricity. With no dust cloud and only light PPE required for outside surface prep work, Vapor Blast improves safety and visibility for workers on crowded offshore platforms.
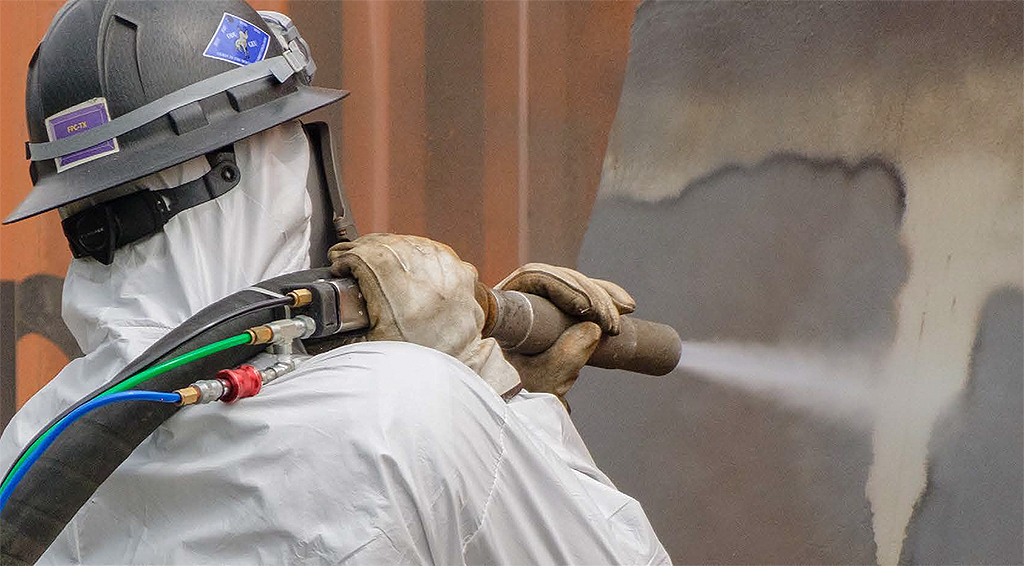
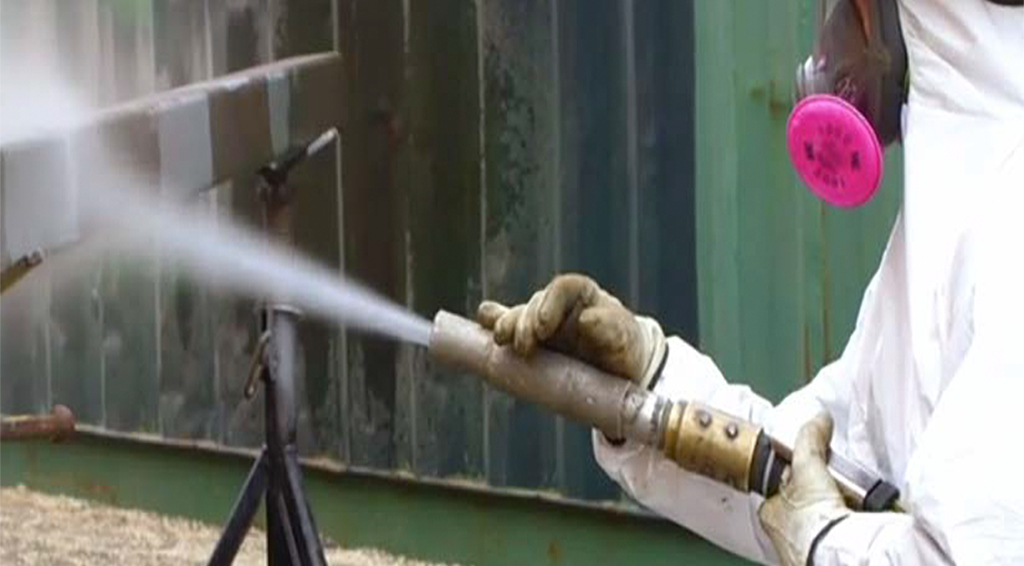
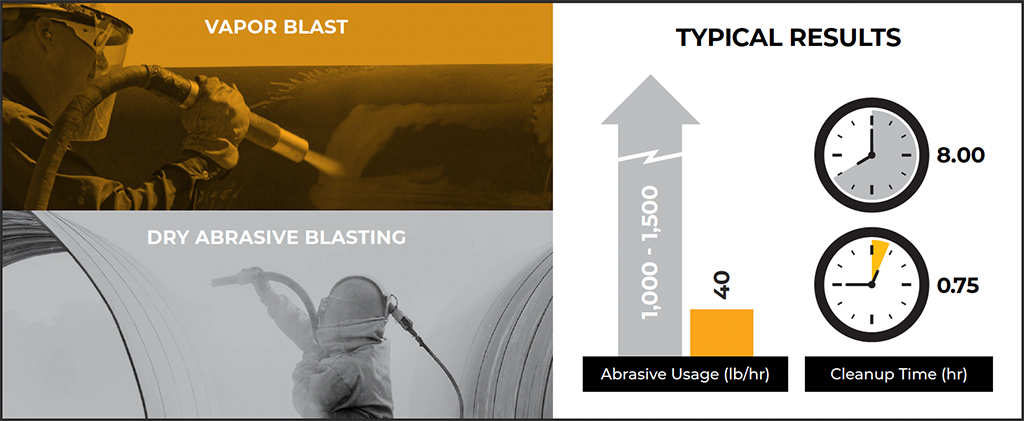
Vapor Blasting vs. Sandblasting
Integrated Coating Services
USA DeBusk provides integrated, single-source Vapor Blast surface preparation and coating services for offshore projects. Application methods include airless spray coating, plural component spray coating, brush, and roller painting. Our NACE-certified technicians and state-of the-art equipment enable us to efficiently handle projects of any scope.
Our coating teams can include Level 2 and 3 NACE-certified inspectors with expert knowledge to assist with coating specifications, non-destructive inspections, assessments, and recommendations. We can develop maintenance coatings plans prioritized by severity, as well as detailed, long-term corrosion mitigation programs to keep assets in peak condition.
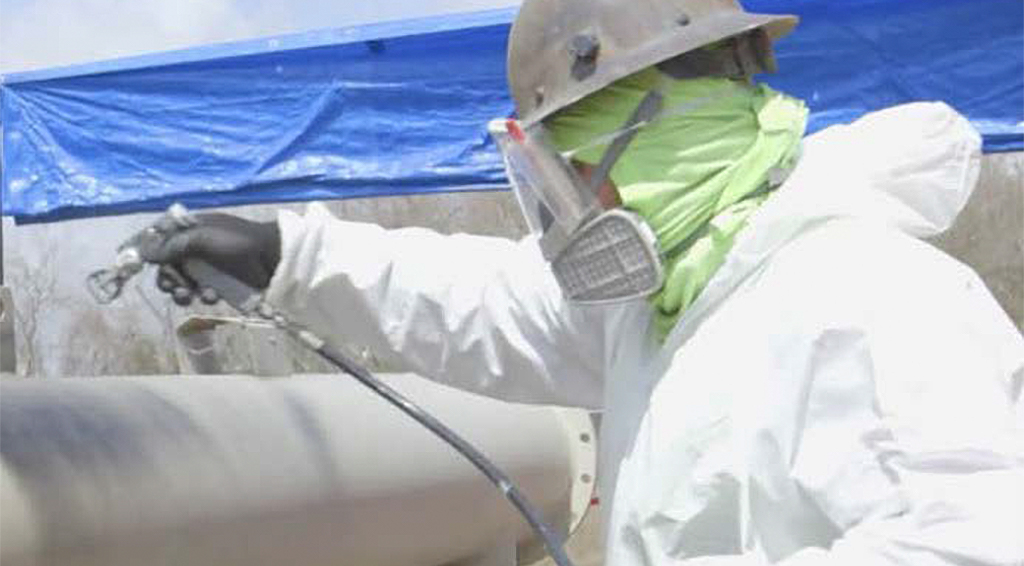
Nitrogen
Nitrogen is a valuable resource offshore as an efficient, inert, and non-corrosive medium for a wide range of applications. Nitro-Lift offers on-site nitrogen generation (membrane) to ensure an on-demand supply of nitrogen gas for well services, purging, pigging, inerting, blanketing, pressure testing, leak testing, and other routine activities on offshore installations.
Nitro-Lift has more than a decade of experience conducting offshore operations for nitrogen pressure testing in new platform commissioning, purging lines for safe repair and maintenance, and pressurizing stabilizer cans, as well as offshore vessel and barge purging.
PATENTED EQUIPMENT
Nitro-Lift brings a distinct competitive advantage for offshore operations with our patented Recirc Nitrogen Units and patented Dry-Pak Nitrogen Membrane Units.
These components address common offshore issues regarding lack of space on platforms and insufficient gas to produce wells and power the platform. Each unit has a 30% smaller footprint than other options, conserving space on crowded platforms.
N2 ARTIFICIAL LIFTING
Nitrogen lifting is used to increase the production of wells that are declining due to diminishing gas for gas lifting. It is also used to increase oil and gas production as part of enhanced oil recovery techniques.
Nitro-Lift developed a process for lifting wells that uses less horsepower, making the procedure a low-cost method with a good return on investment.
The process was first demonstrated in 2012, successfully lifting a dead well with nitrogen and turning a well that was slated for plugging and abandonment back into a successful producer.
HYDRATE REMEDIATION
Gas hydrates can form blockages in subsurface flowlines and pipelines. Nitro-Lift conducts offshore operations for hydrate remediation, restoring flow and increasing safety.
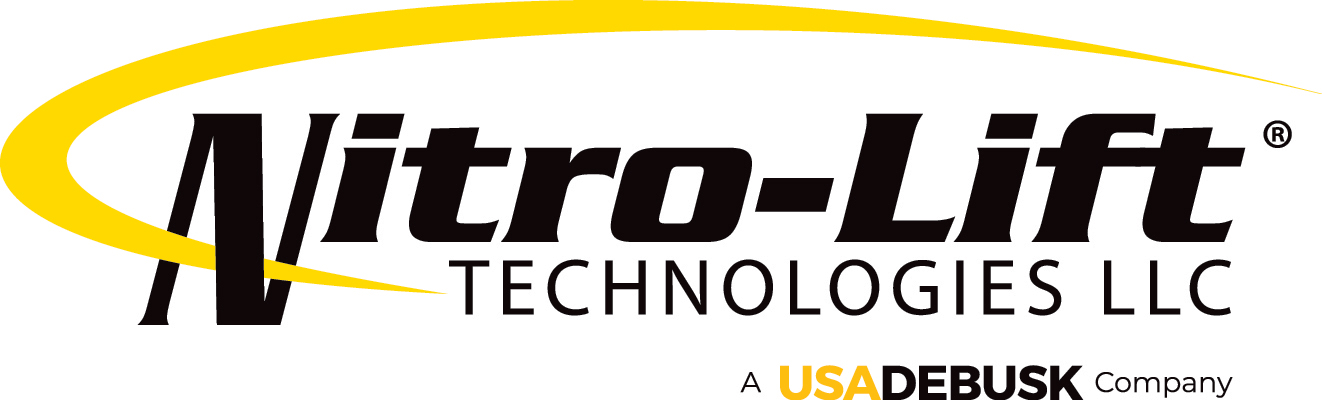
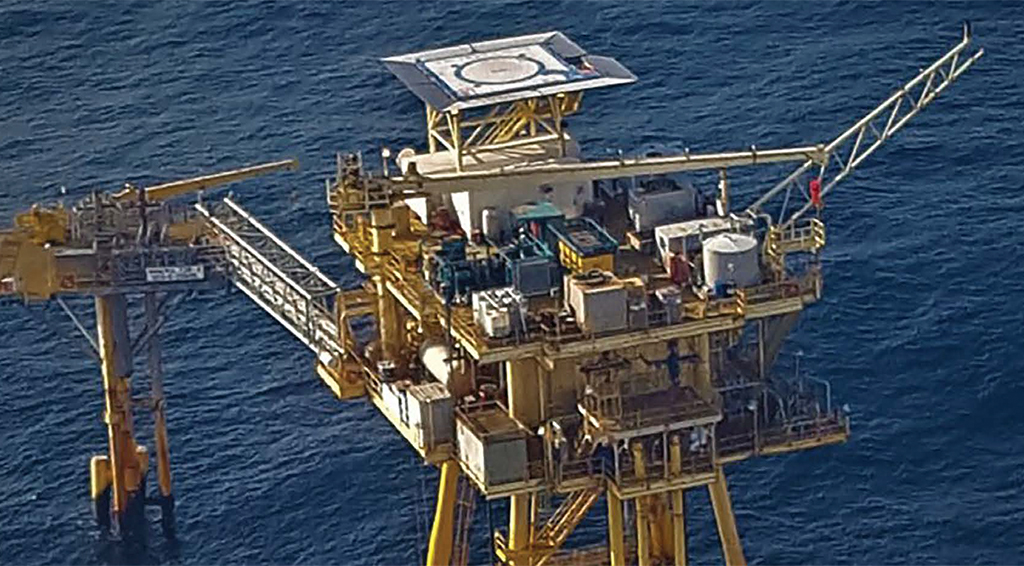
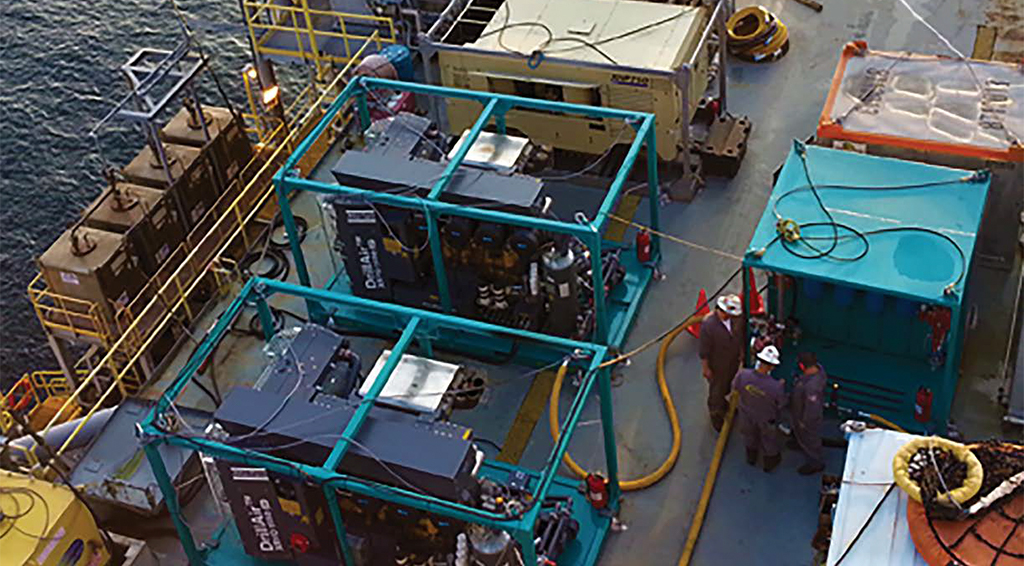