Single-Source Solution, Multi-Service Value
For the first time, the critical services and support needed for safe, efficient hydrotreating, reformer, and hydrocracking reactor turnovers are available from a single source: REAX™ services.
Turnkey Reactor Support
USA DeBusk offers best-in-class services for cleaning and clearing reactors, along with catalyst services, nitrogen, and emission controls to facilitate safe, fast, cost-efficient turnovers.
Functioning as one team allows tasks to proceed seamlessly and transitions to be managed more effectively. As a result, delays can be eliminated and overall project timelines minimized. What’s more, synergies and efficiencies in time, equipment, and manpower lead to quantifiable project cost savings.
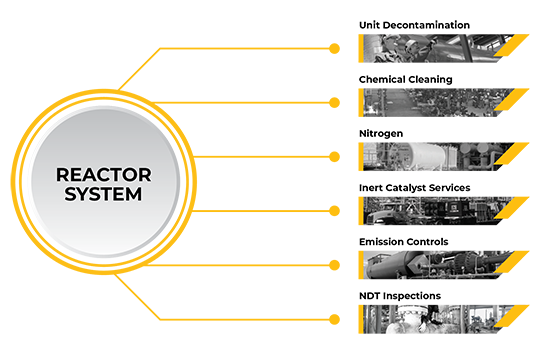
REAX™ Advantages
For reactor owners and operators, project oversight is simplified with a single point of accountability, streamlined communication, and simplified project administration, billing, and reporting.
Most importantly, safety becomes a unified commitment, with focused leadership and all participants following the same stringent, clearly delineated standards.
Rigorous, uniform safety
Faster timeline
Schedule dependability
Single-source efficiency and accountability
Cost savings
Best-practice integration
Effective communication
Planning and execution expertise
Patented chemistries and systems
Automated technologies
Complete emission control
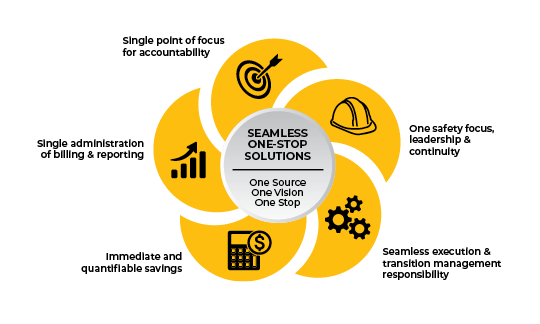
REAX™ Services
Our turnkey, multi-service line solutions for reactor turnovers include these advanced technologies.
Reactor Chemical Cleaning
Patented Online Process
REAX™ services include patented, proven technology to clean hydroprocessing unit reactor systems. Our process uses specially engineered chemistries to remove hydrocarbon deposits and degas reactors online, during the early stages of a process unit shutdown.
The process removes LEL, H2S, benzene, and other noxious gases from catalyst reactor systems. It is effective with hydrotreaters, reformers, hydrocrackers, and many media-containing vessels with dry gases.
Fast, dependable shutdown
Superior cleaning of highpressure equipment
Eliminates or reduces flushing and hydrogen hot stripping
Decreases nitrogen usage
Reduces venting and flaring
No harm to catalysts
Chemistry is compatible as feedstock
Improves catalyst regeneration
Increases spent catalyst fluidity
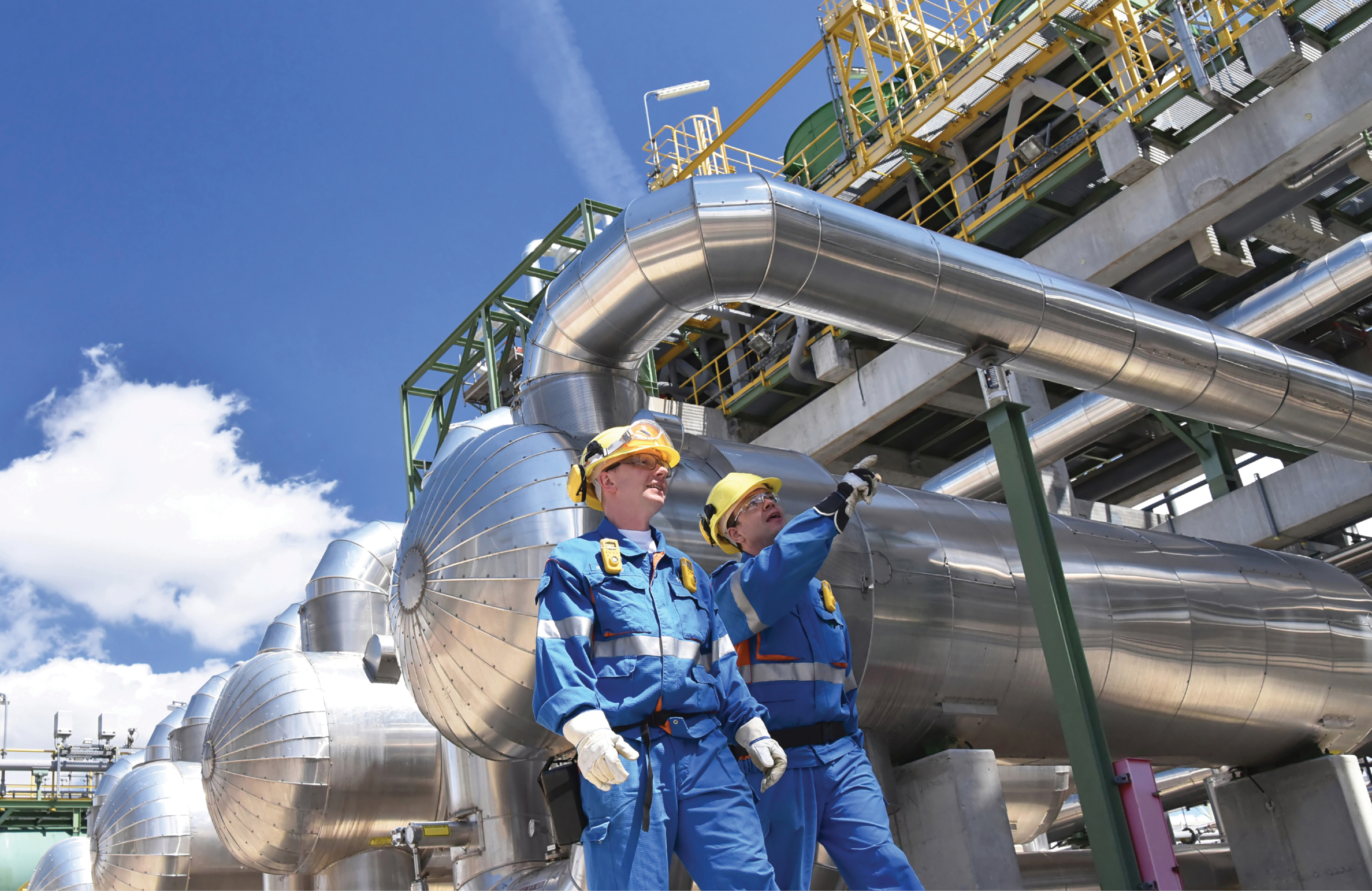
Effective, Efficient
The cleaning process is designed by reactor specialists to integrate seamlessly into high-pressure catalyst reactor shutdown procedures and produce results that are efficient, effective, and predictable. The process decreases flushing and sweeping, eliminates hydrogen hot stripping before cooldown, and minimizes subsequent nitrogen purging.
Catalyst Friendly
REAX™ reactor cleaning has no harmful effects on catalysts and removes hydrocarbon contaminants from the catalyst surfaces. If the catalyst is to be removed and regenerated, it improves the dumping process by increasing spent catalyst fluidity. If the catalyst is left in place, enhanced cleaning can decrease pressure drops and increase catalyst activity.
A Safer Option
The process enhances safety and compliance by reducing total time on site, decreasing or eliminating confined space entry for cleaning, and minimizing venting and flaring. Optional no-exotherm chemistry enhances safety in potentially volatile applications.
Saves Time & Money
As an online process with fast-acting chemistries, the process yields substantial cost savings from shorter cleaning times and reduced usage of hydrogen and nitrogen. It produces cleaner high-pressure equipment compared to traditional methods, reducing the delays and costs of further mechanical cleaning once the unit is opened.
Veteran Expertise
Reactor cleaning projects are planned and executed by teams of experts with extensive experience in chemical cleaning, reactive chemistry, and plant operations. From degreed engineers in project planning to veteran supervisors and technicians in the field, we apply decades of experience to ensure your reactor shutdown proceeds safely and efficiently.
Inert Catalyst Services
Total Catalyst Support
Specialists provide turnkey catalyst services, including mechanical isolation and closure, surface preparations, unloading/loading of catalyst, separation of spent material for regeneration, tray replacement and revamps, and transportation services. Our management team and crews have decades of catalyst-handling experience.
Technical innovations include remotely controlled robotic catalyst removal, CO2 gas expansion fracturing to dislodge fused catalyst deposits, purpose-built vacuum units, and unitized support equipment for fast mobilization. Our industry-leading safety systems feature Life Support Units with biometric personnel monitoring for technicians entering confined spaces.
Best-in-class safety
Unloading and loading of catalyst, wet or dry, under inert or non-inert conditions
Robotic catalyst removal
Purpose-built vacuum units and support equipment
Multi-crew, round-the-clock capabilities
Reliable, modern, company-owned equipment
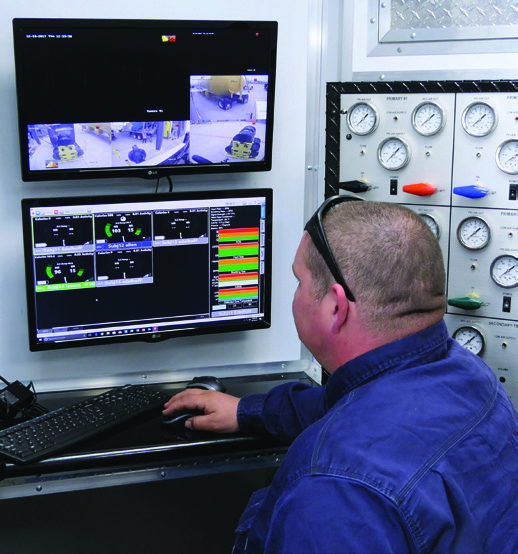
Nitrogen
Mobile N2 Supply
Nitro-Lift services support reactor turnovers with mobile nitrogen systems to produce hot and cold nitrogen for unit decontamination, chemical cleaning, and catalyst changeouts.
Our proprietary Skid Mounted Vaporizer Units (SMVU) produce nitrogen gas at flow rates of 90,000 SCFH and pressures up to 225 psi. This “Green Technology” vaporizes liquid nitrogen using steam to eliminate diesel fuel usage and ensures zero carbon emissions. These units have a smaller footprint than traditional pumpers and require less manpower to operate. In some applications, they eliminate the need for hot work permitting.
Liquid and membrane technologies
Provides any volume, flow rate, pressure, or temperature
SMVU has zero carbon emissions
Large, diverse fleet
Qualified and experienced teams
Transportation and storage units
![DEB Nitrogen Solutions Sales Sheet - 102023[2]](https://usadebusk.com/wp-content/uploads/2023/10/DEB-Nitrogen-Solutions-Sales-Sheet-1020232.jpg)
Emission Controls
Complete VOC Management
Our teams provide vapor control and processing during all phases of reactor decontamination and cleaning. Each project is custom engineered, and our equipment fleet includes the most advanced mobile thermal oxidation units and vapor scrubber systems. To assure regulatory compliance, our coupled thermal oxidizers/scrubbers exceed the requirements of both NSPS Subpart Ja & Ja, BACT, and state agencies.
Vapor Control SMEs remain onsite for the entire project to ensure all systems remain vapor tight and all emissions are mitigated. Comprehensive environmental compliance reporting and support is included. Packets and certifications are provided to the client or environmental agency at the completion of the project.
Controls all potential vapor hazards, including LEL, H2S, and high pressures
Reduces client’s carbon footprint
Meets or exceeds regulatory requirements
Reduces risks of damage to equipment and infrastructure
Allows turnover activities to proceed efficiently
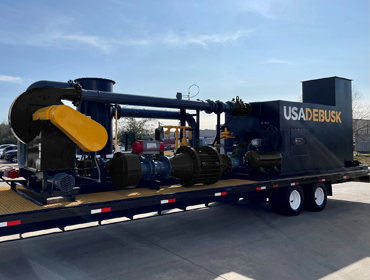