Turnkey, Custom-Engineered Solutions
Enhanced safety
Reduced turnaround duration
Lower costs
A single point of contact and responsibility
Reduced offsite exposure and transportation risks
Minimized handling damage
Turnaround Management & Service Line Capabilities
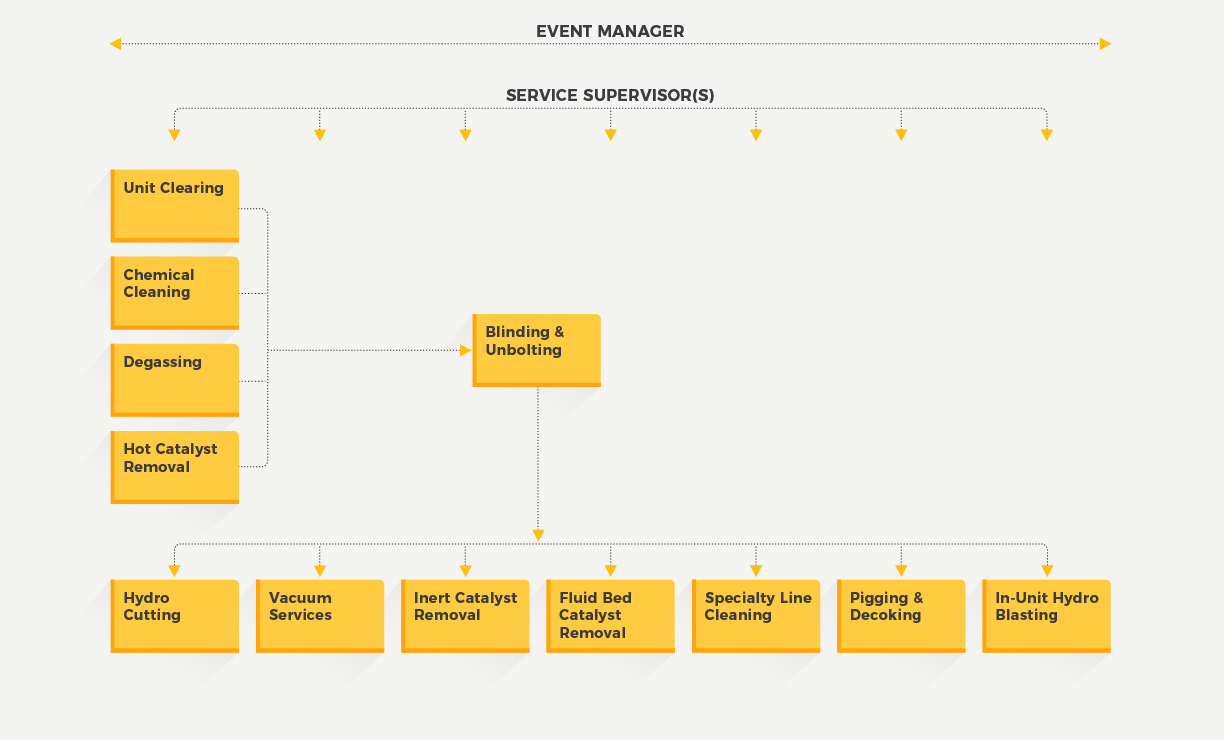
- Unit clearing
- Chemical cleaning
- Degassing
- Hot catalyst removal
- Fluid bed catalyst services
- Fixed bed catalyst services
- Inert catalyst services
- In-unit 10-40,000 psi hydro blasting
- Pigging and decoking
- Precision hydro cutting
- Vacuum services
- Specialty line cleaning
- Specialized FCC unit services
- Specialized Coker unit services
- Automated technologies for all units
- Water recirculation for hydro blasting and pigging & decoking
- Flareless turnarounds for all units
- MSS vacuum trucks for all units
Unique Resources, Superior Results
Turnkey, Multi-Service
We provide the broadest range of specialty, high-value service lines and the ability to execute a larger scope of turnaround services. We also handle routine tasks, such as moving and connecting hoses, so your personnel don’t have to.
Best-in-Class Safety
We operate according to the industry-leading safety guidelines. We develop project-specific safety plans incorporating both customer and USA DeBusk guidelines, make extensive use of automated technologies, and have dedicated Safety professionals onsite at all times.
Strategic Planning
Our Event Manager and turnaround teams work with your engineering, operations, maintenance and HSE personnel to clarify the scope of work, identify potential problems, and develop safe, effective solutions to meet your objectives.
Synergy
With the ability to command multiple service lines and resources, we take advantage of efficiencies in utilizing equipment and personnel, saving time, reducing costs, decreasing our overall footprint, and ensuring consistent, quality results.
Event Management
A highly experienced Event Manager participates in the the earliest stages of turnaround planning, provides top-level management, coordinates field-level supervisors, and streamlines customer communications.
Automated Technologies
Extensive automation throughout our service lines increase speed, improve precision and productivity, and mitigate safety risks.
Sustainability
Our procedures protect people and the environment. We offer enhanced containment, water recirculation and on-site filtration technologies to conserve resources and reduce waste.
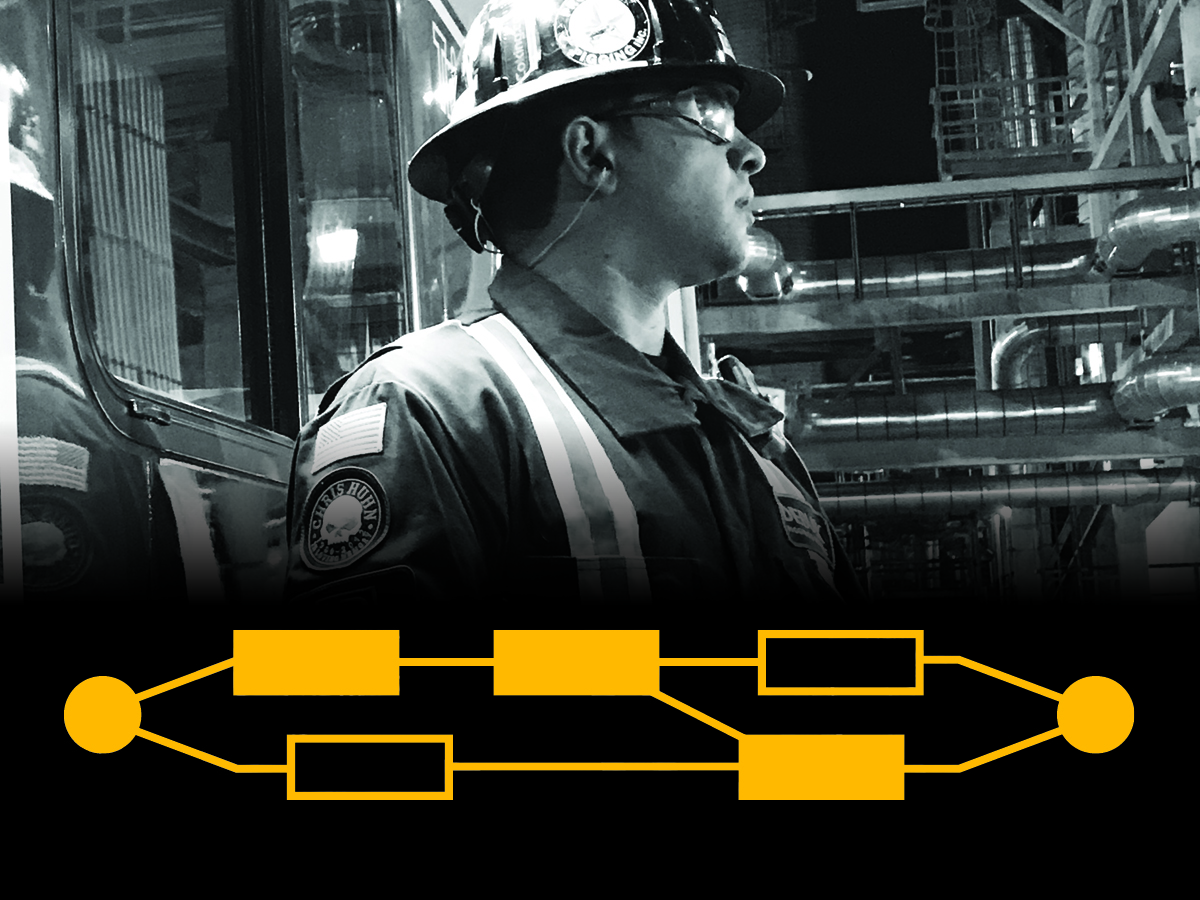
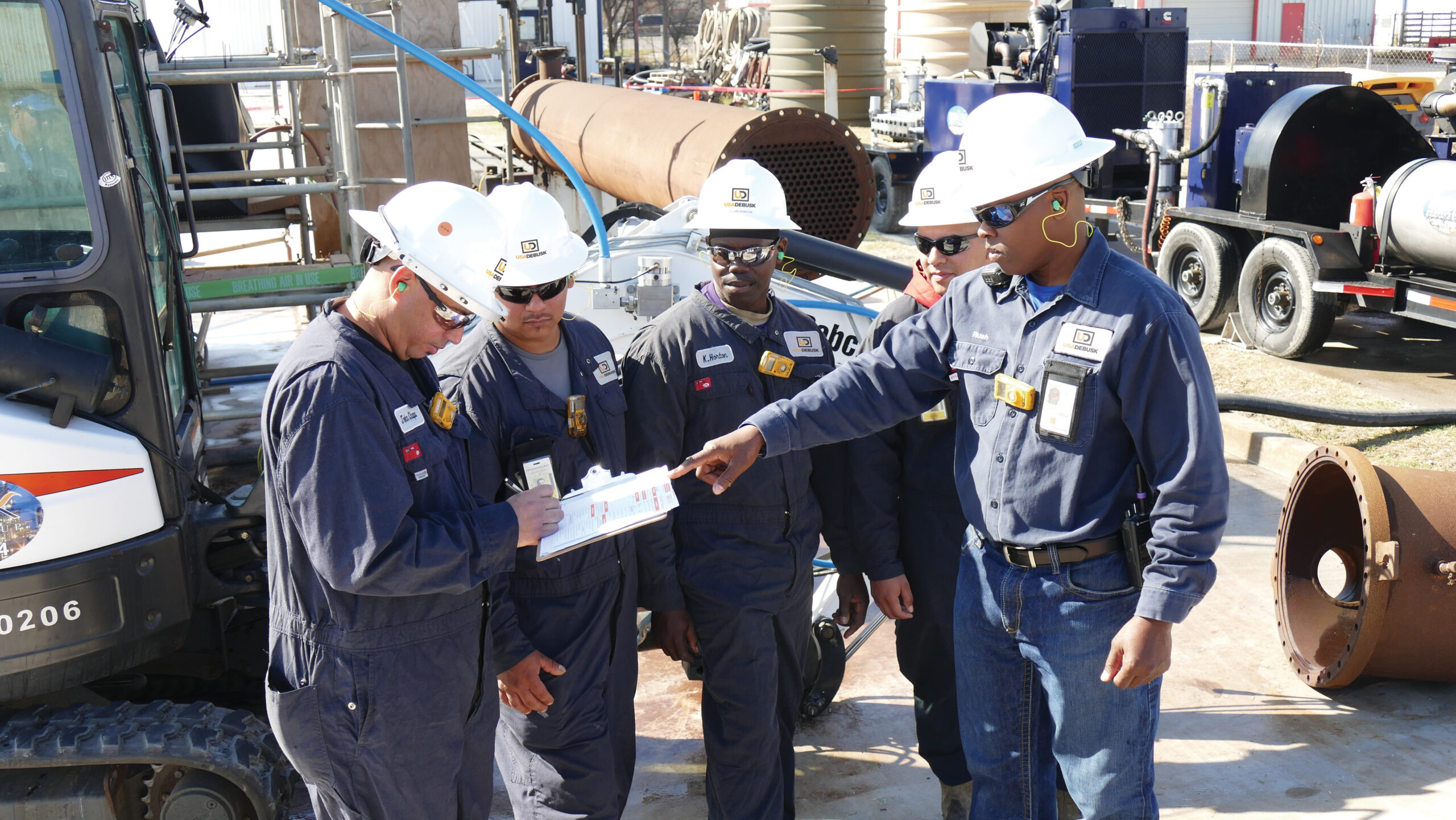
Safety
We develop a project-specific safety plan that incorporates both customer and USA DeBusk guidelines.
As a multi-service-line provider, we are able to establish and enforce more consistent safety practices for all work.
Top level participation, including senior USA DeBusk management and Event Manager
Safety trackable QR codes on each employee ID badge link to cloud-based records of certifications and training; customers can check the status of any employee in real time
Safety professional(s) on-site full time
Automated technologies reduce risks
Specialty Service Highlights
Unit Clearing
Opens the unit efficiently, saving days on the turnaround critical path
Safe for personnel and equipment
Pre-engineering to develop detail drawings and timelines
Proven, predictable results
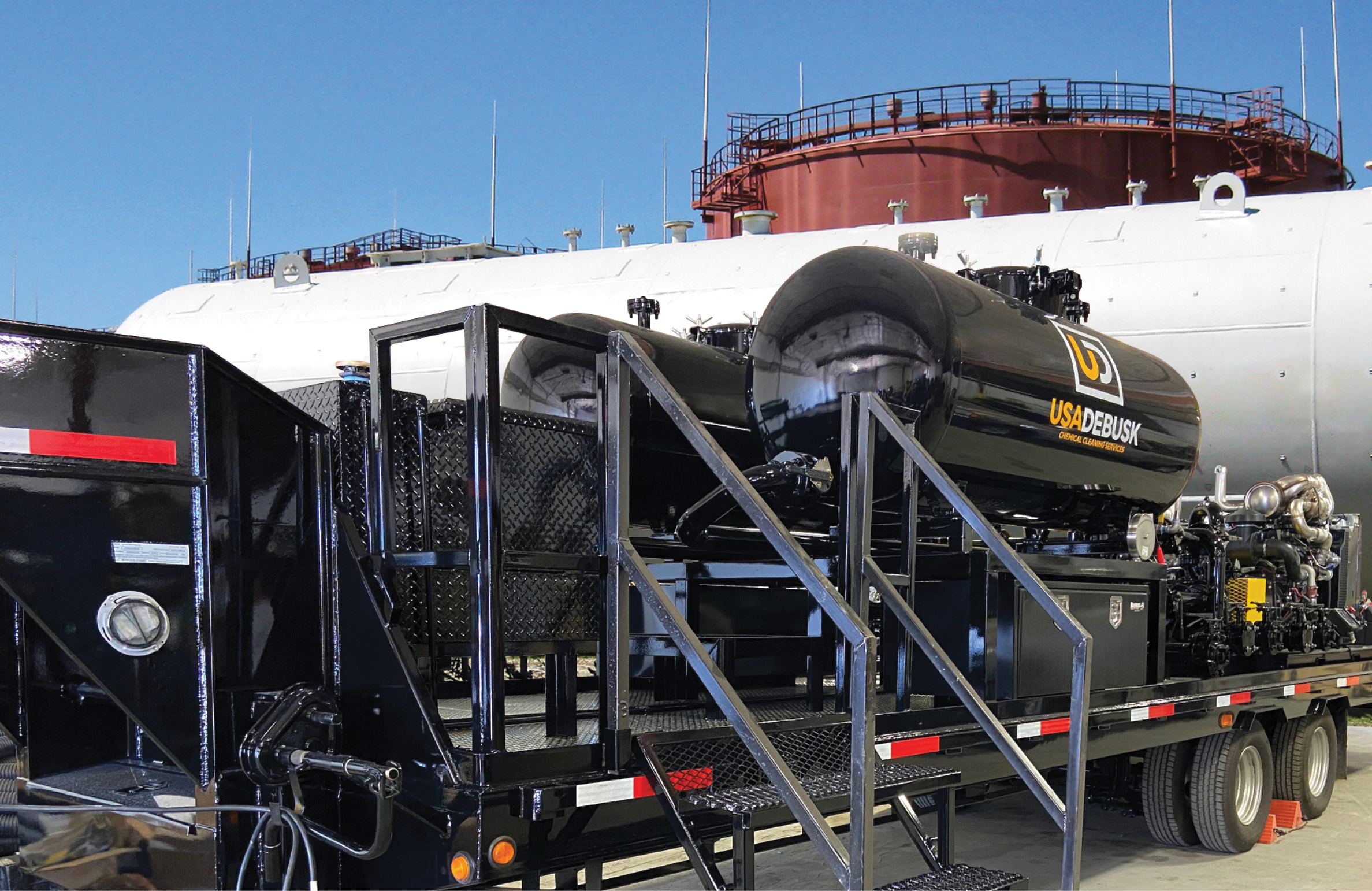
Hot Catalyst Removal
1,250°F (677°C) vacuum technology
Eliminates cooling time
Savings on catalyst purchase and disposal
Operational yield support, transloading

Inert Catalyst Services
Safety innovations include real-time biometric monitoring
Catalyst Removal Amphirol (CAROL), the only robotic solution in the U.S. for unloading catalyst from inert reactors
Cardox CO2 gas expansion fracturing to dislodge fused catalyst
Vacuum units and other equipment purpose-built for catalyst handling
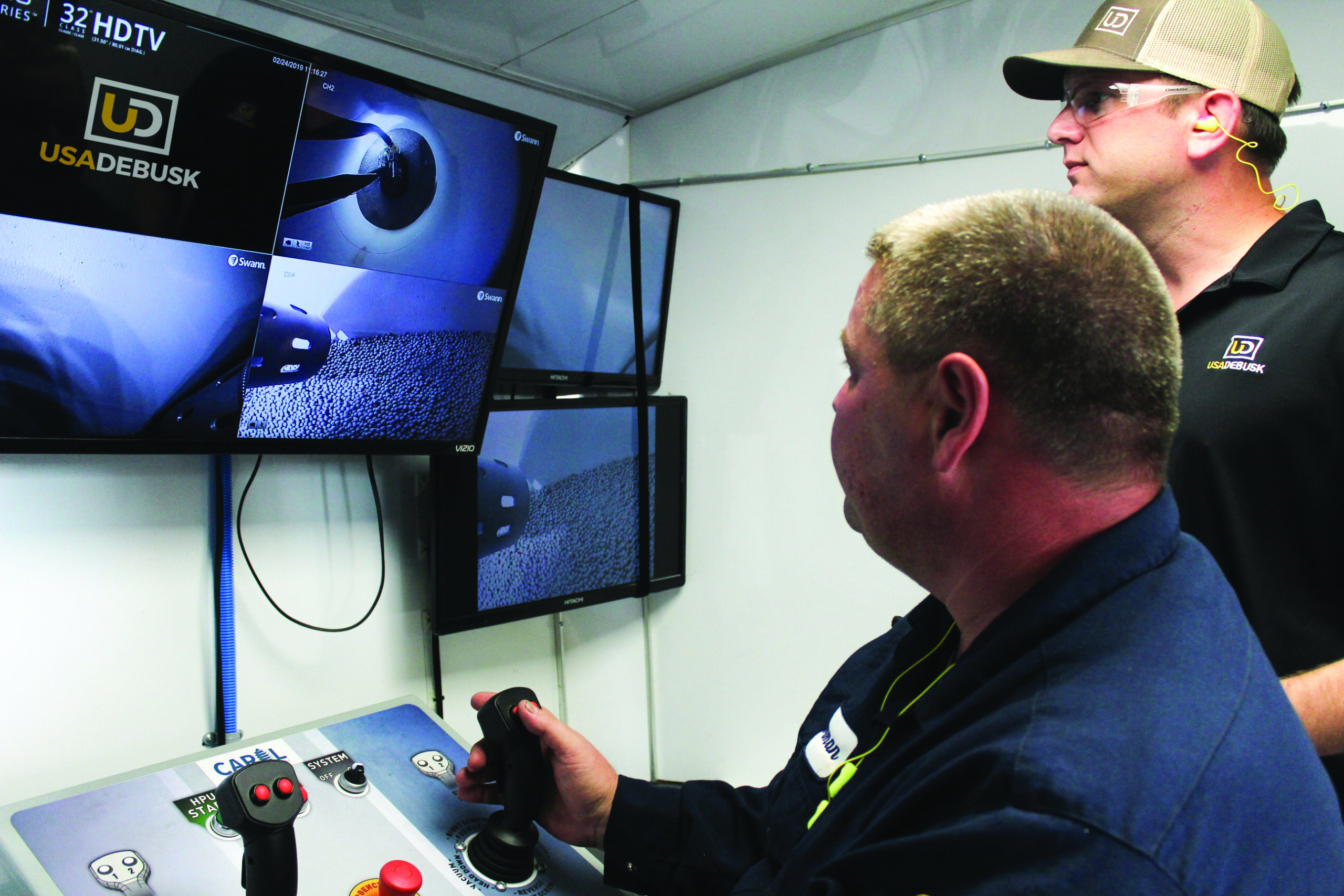
Pigging, Decoking & Filtration
World’s largest fleet of TriMax™ triple pumping systems that increase productivity by 50%
Advanced electronic controls, automation and video monitoring
The industry’s most diverse selection of decoking pigs
Closed-loop effluent filtration
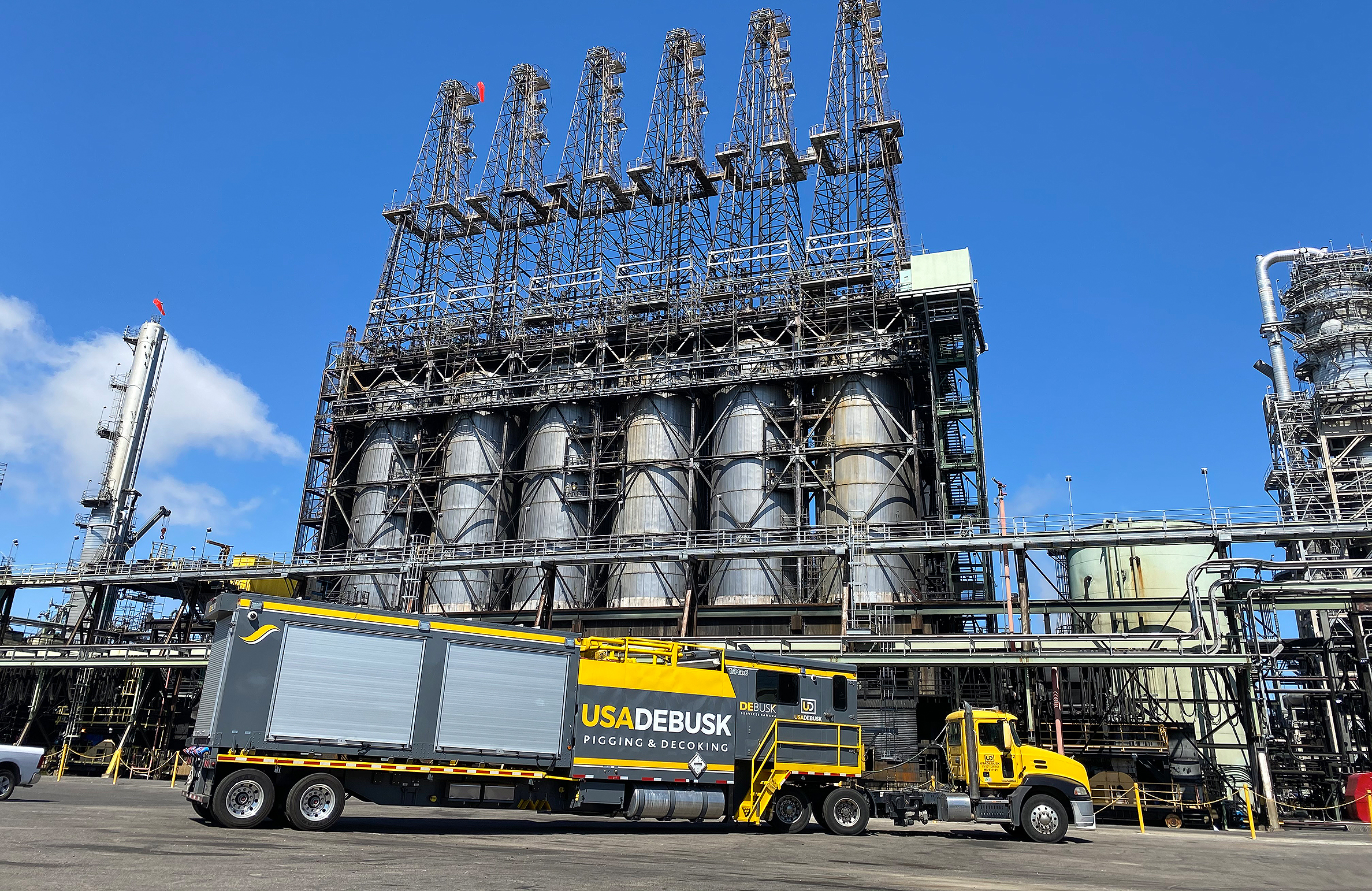
Specialty Line Cleaning
Automation for safety and productivity
Custom engineering to apply properly sized hoses, nozzle configurations, pressures and cleaning speeds for each line
Containment of coke and water
Highly trained personnel
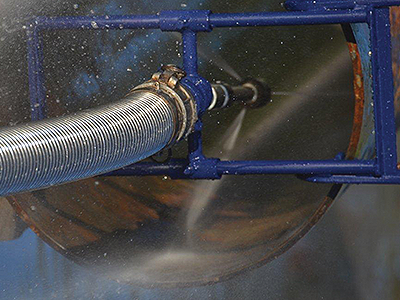
Hydro Cutting
40,000 psi water
Fully automated operation
Specialty tracks
Dedicated hydro cutting teams
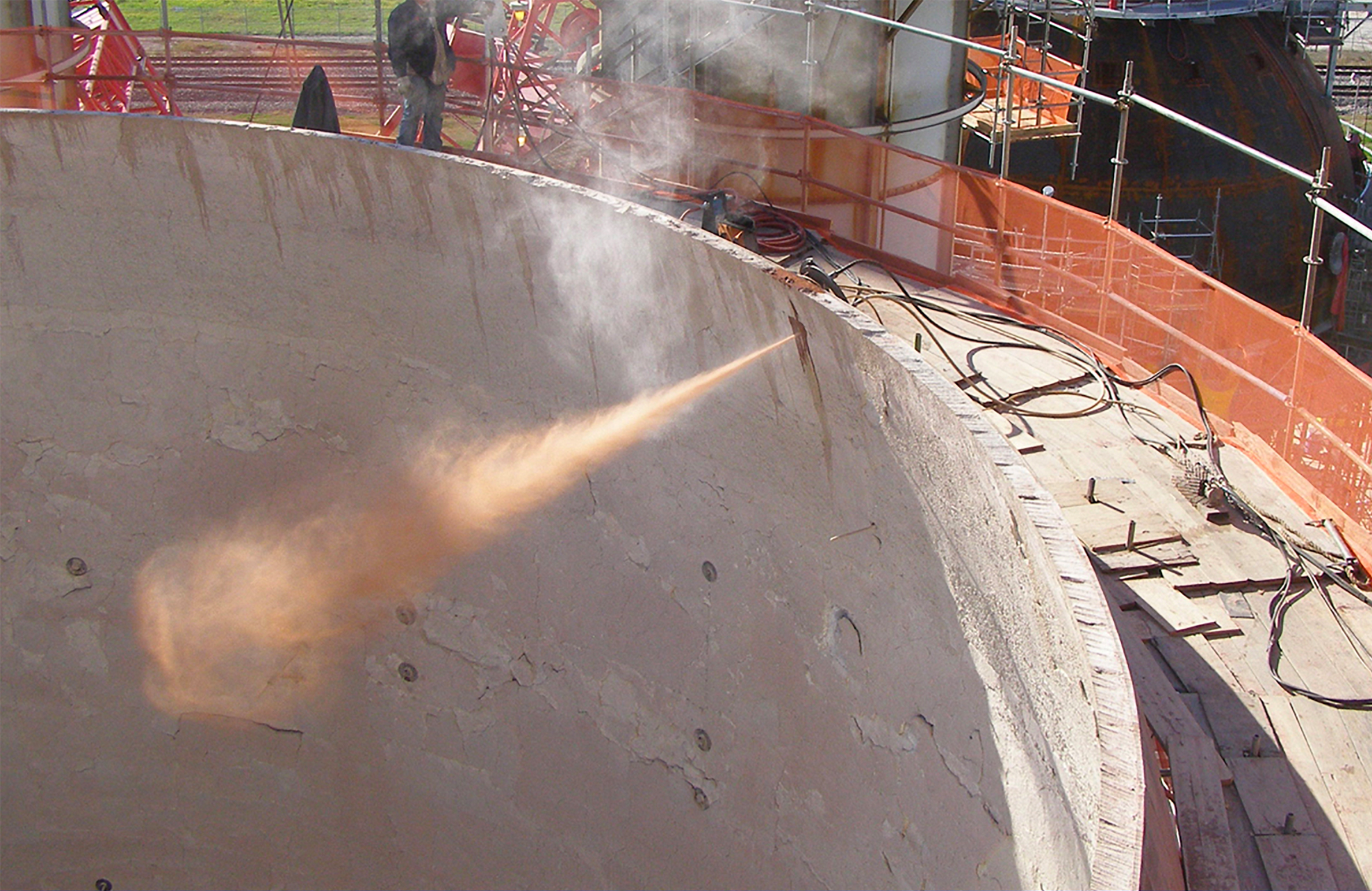
Hydro Blasting
Units up to 40,000 psi
In unit and pad
Automated technology
lab management
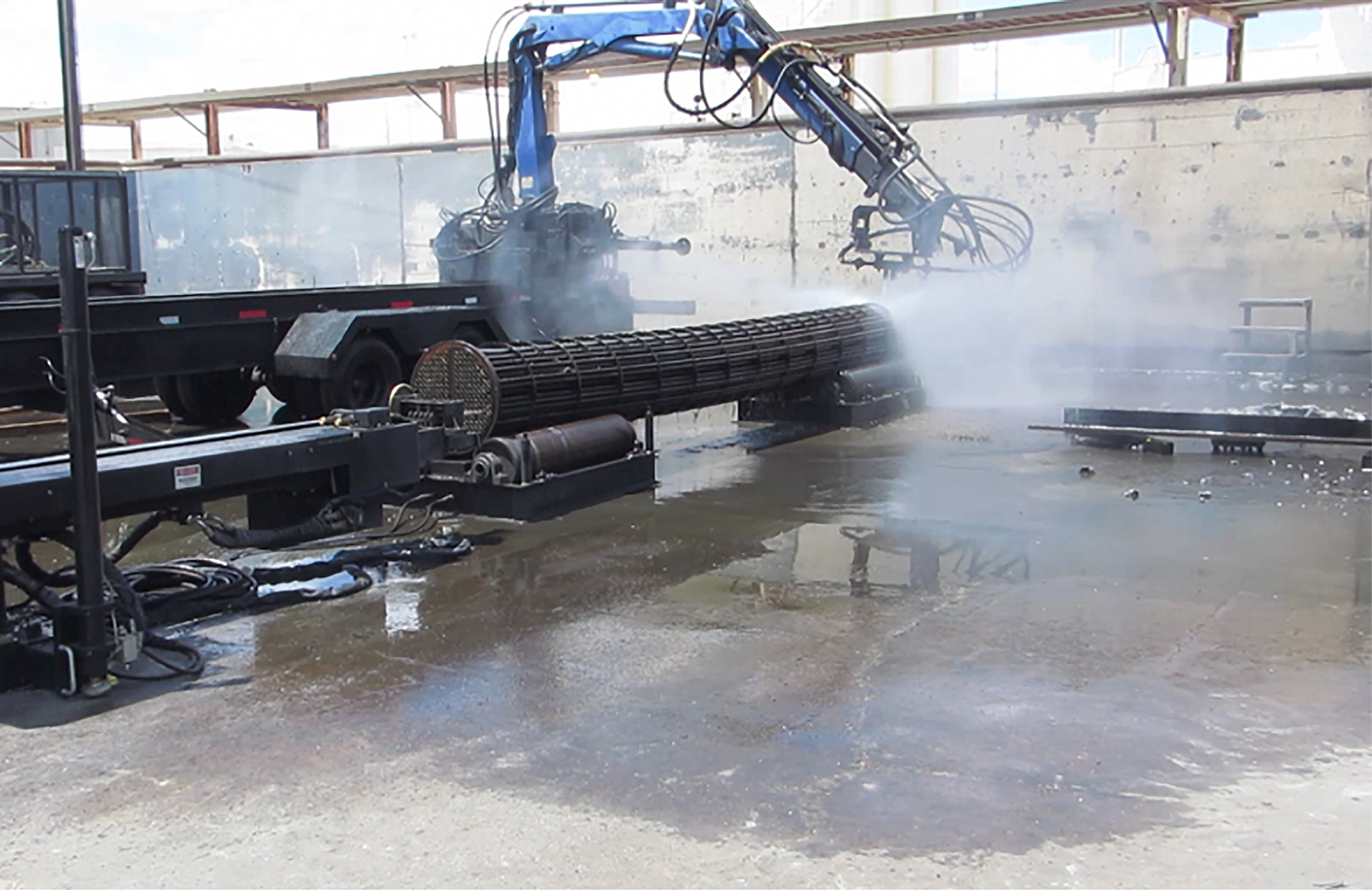